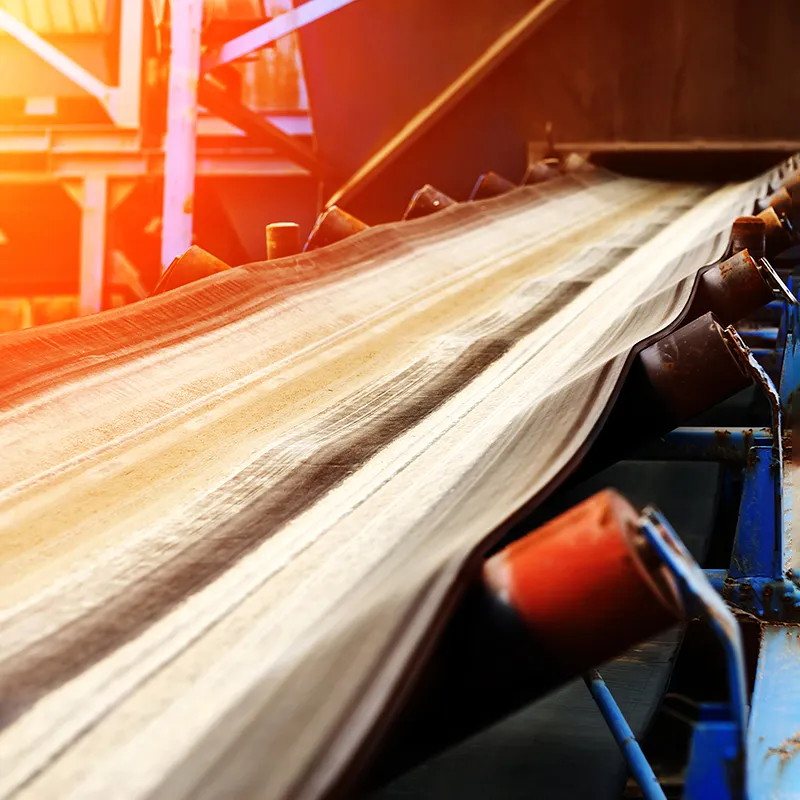
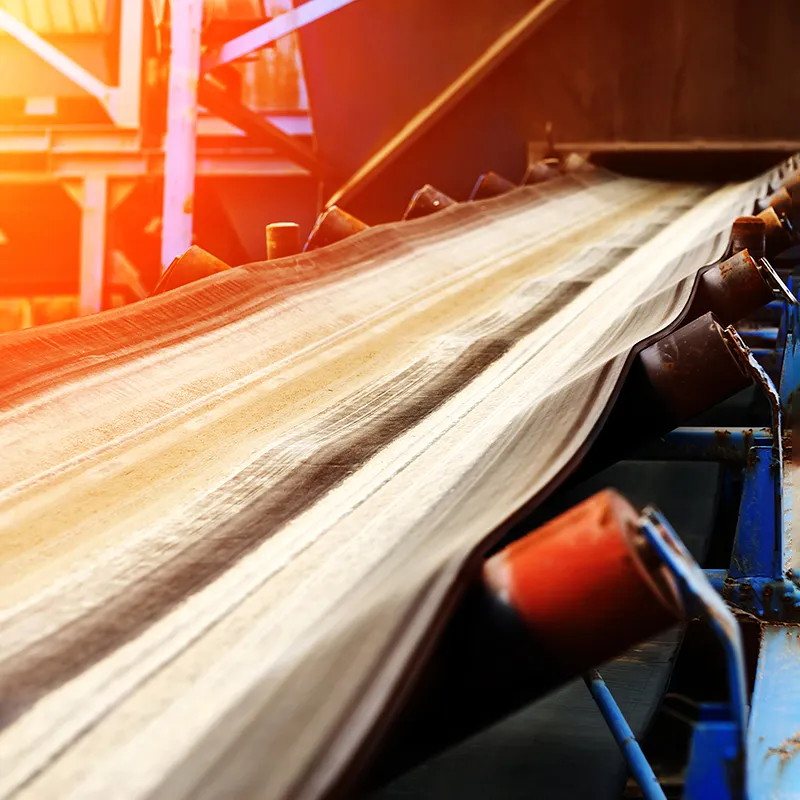
Becker Mining South Africa’s range of safety and communications systems encompasses the BRS2 Beltrip Detection System, using its real-time loop diagnostics to continuously monitor the belt’s health and in the event of a rip, stops the belt and reduces any further damage and downtime.
Becker Mining South Africa deployed in excess of 25 systems to one of the leading coal mining groups in South Africa, as well as 35 systems to a prominent Platinum mine in Africa. Becker Mining South Africa has been successful in implementing the BRS2 system to protect the longest over-land conveyor globally, exceeding 55 kilo-meters.
The Becker BRS2 system allows the end user to plan in advance for sensor loop maintenance work, it does not require to stop the belt while scanning, all measurements are collected while the belt is running at full load, can be used for both steel cord and textile belts, on new or used belts.
The remote access capabilities of the BRS2 system allowed these customers to monitor the status of their belts remotely by making use of the integrated Modbus and / or TCP/IP capabilities of the system. With the large LCD screen and system status lights on the BRS Master panel, belt operators are able to determine the system status at a glance and interrogate event logs, loop statuses as well as belt trip causes with ease, reducing belt down time.
The new Becker Mining Systems Belt Rip Detection System BRS2 has been developed to help increase the productivity of conveyor belts by detecting belt rips as soon and as reliable as possible. To monitor steel cable and fibre belts, inductive loops need to be embedded in the belt. Once installed the BRS2 will detect the loops on the conveyor, define and number the loops and create its own image of the belt and its loops in real time.
With some of the BRS systems being deployed in excess of 15 years, the system offers a low cost of ownership to the end user. The high-quality German Engineering of the system allows for deployment in harsh environments both in underground as well as surface applications.
Integration with the existing belt starter panels allowed the end users to take advantage of the BRS2’s capability to continuously monitor the belt speed, as well as belt direction forward or reverse. The BRS2 system monitors these parameters to ensure compensation for belt slippage, belt stretch as well as directionality for effective rip detection.
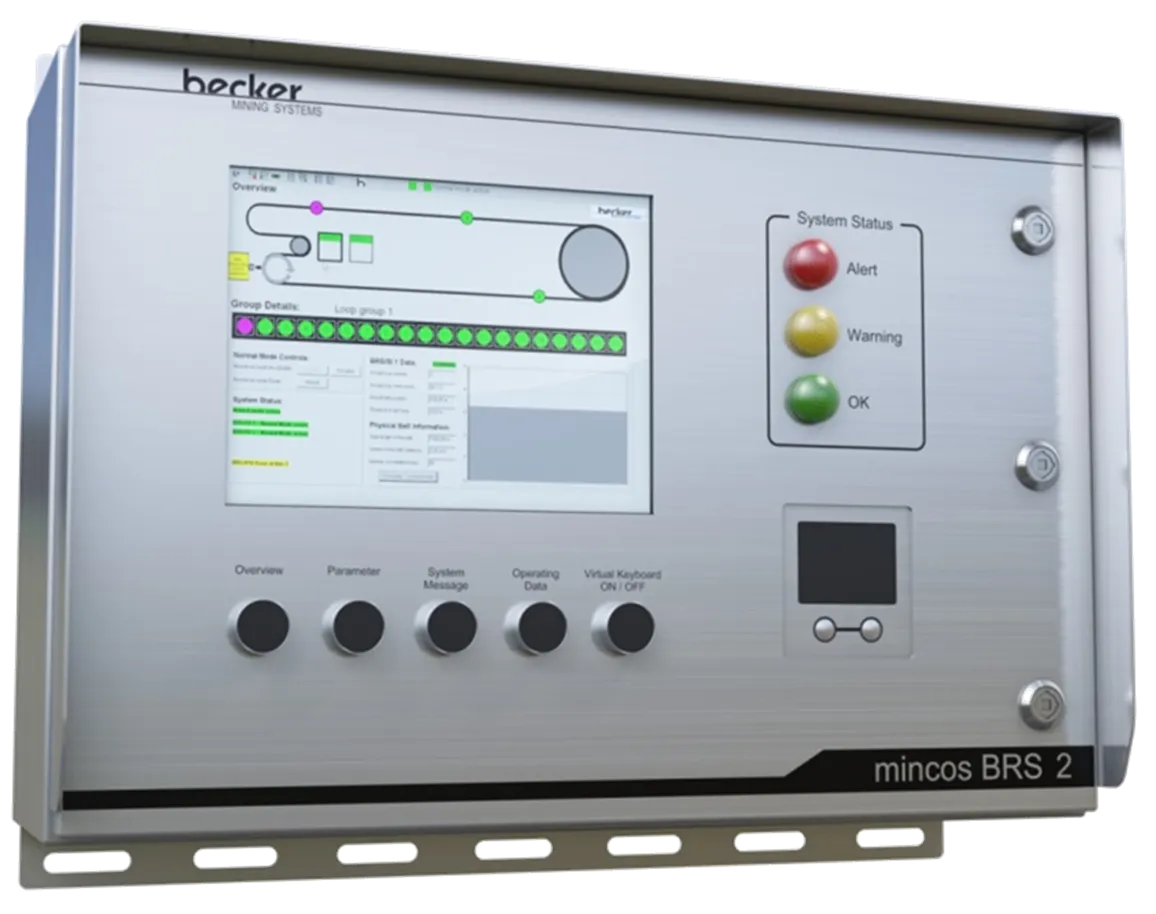